Experiment Description
Currently, biomass combustion (Figure 1) faces a strong worldwide shift from high quality wood chips to problematic residues from industrial production, food industry and agriculture such as coconut shells, olive seeds, cotton stalk, etc. These fuels are challenging for currently applied technology due to low ash melting temperatures, high ash contents, low calorific values, high content of sulphur, chlorine and other elements causing corrosion. For end user UAB ENERSTENA it is critical to expand the current technology to both problematic fuels and markets outside Europe.
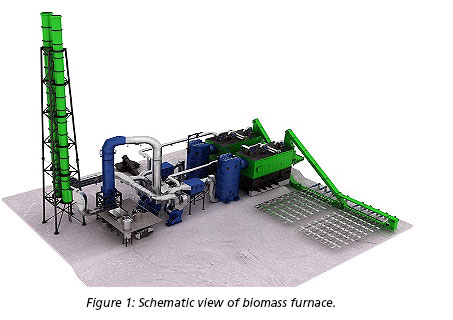
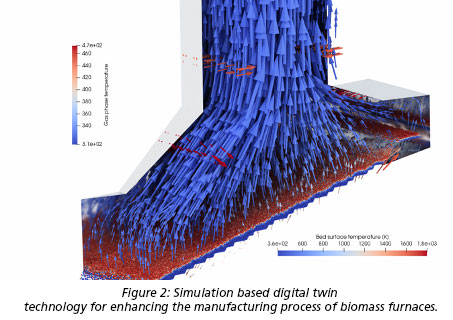
In order to decrease production costs and time engineers often opt out for "cut & paste technology" of already proven components and systems from previous generations which offers only little potential for innovation and optimisation that, however, is required for burning problematic residues. Therefore, the objective is to utilize develop sustainable and optimised production technology of biomass furnaces for problematic fuels leading to an efficient generation of energy at reduced emissions.
This will be achieved by a simulation-based digital twin (SBDT) based on a first principle models from physics, chemistry and thermo-fluid dynamics and thus, represents an integrated multi-physics and multi-scale virtual replica of a furnace.
Technical Impact
The experiment will deliver a workflow integrated in the Cloudifacturing infrastructure. It covers the entire processing chain between input and analysis. In order to facilitate the application of a simulation-based digital twin at the end user UAB ENERSTENA, the consortium will address the following issue in the workflow:
Pre-processing: A basic set of input parameters will be defined in close collaboration with UAB ENERSTENA. This input will be entered into a web interface and then processed by the workflow to generate a case setup for the digital twin before the case will be executed on HPC resources.
Post-processing: Execution of the digital twin produces large data sets. The workflow processes and analyses this data automatically to create a report that extracts the main production indicators for the furnace.
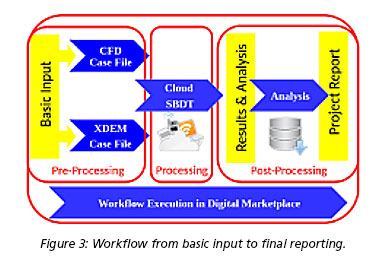
Economic Impact
The above-mentioned measures are expected to shorten the production period by 1-2 months, to acquire app. 50 new clients resulting in a 75 % increased turnover for UAB ENERSTENA. The workflow, which will be developed by Wikki, is a significant enhancement of the XDEM software and is considered as an innovative business model for Wikki that has a strong potential to grow and to be applied for grate combustion technologies with a market share of 79 %. In addition, with app. 200 manufacturers of biomass combustion plants in the European community, there is a huge demand for the workflow technology developed. Furthermore, the developed technique will be made also applicable to medium and small scale ovens down to domestic burners. Exploiting these opportunities will increase the turnover of Wikki by app. 25 %. Once this application has been cloudified successfully, it is envisaged to map the technology to other applications in the thermal processing industry, iron making and food industry in which the cost for potential clients, in particular SMEs, to use the software in-house is too high due to the investment in hardware and training of staff.
Experiment Partners
Competence Centers
Digital Innovation Hub
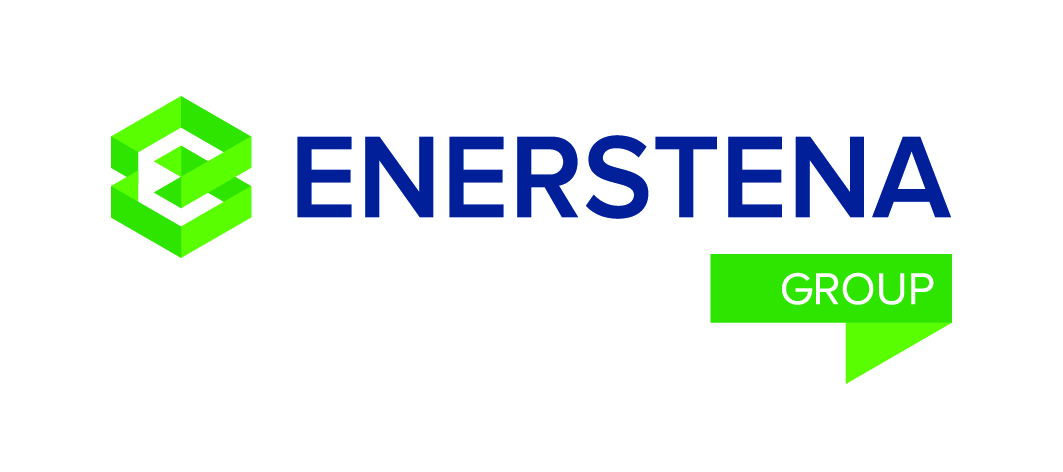
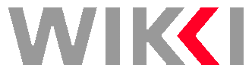
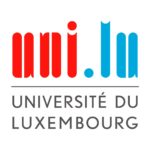


