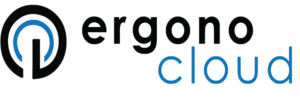
Despite the increasing technologization of our working world human labour cannot be replaced in the future. But the question is, how can modern technology and physical work be compatible in the future and how can technology help to avoid human failure?
Experiment Description
In-Vision Digital Imaging Optics GMBH manufactures smart opto-mechatronic systems, “Light Engines” for leading 3D printer manufacturers. Their quality is crucial for them and also for the end-users. Light engines consist of 200+ single parts with many of them being highly sensitive to contamination and mishandling (optical elements, PCB, DMD), the assembly process is done manually, based on very detailed work instructions and are therefore susceptible to human failure. This risk can be minimized by employees having the optimal working position to carry out their tasks.
To achieve this, ErgonoCloud experiment aims to build on ViveLab's existing solution, which increases production efficiency by optimizing production processes, reducing losses and improving quality. It achieves this by determining the position of employees in relation to machines, tools and each other during the production process, the postures they should take and movements they need to make as they perform their tasks. Digital modeling and thorough international standard evaluation of manufacturing and quality assurance is done by collecting data from sensor-equipped garments which analyze the movement of workers and the efficiency of the work process.
Technical Impact
During virtual verification, the working environment, design workstations and work processes are optimized. Currently and without the use of CloudiFacturing HPC resources both the movement optimization of the workforce as well as the real-time quality measurement and prediction modules are not realizable at all.
By cloudifying ViveLab’s ergonomic software the Ergonocloud experiment makes the seamless integration of movement data, product related information (components, assembly steps), ergonomic optimization, visualization and human interaction (through the Dynamic electronic Working Instruction) possible.
Economical Impact
From the project the partners expect less customer requests within guarantee coverage (-50%), less 3rd party products used (-15%), extreme savings in administrative and assembly workforce (-33%) (all customers have customized light engines, the preparation and readjustment of the production line to produce low quantities because of previous quality complaints is extremely time consuming and ineffective). Since the assembly of a light engine takes approximately 15 hours per engine, involves 3 differently skilled people and costs about USD 1500-7000 (source: competitor website), even minor manufacturing process modifications and adaptations would result in large performance improvements (15%).
By Cloudification Ergonocloud experiment also aims to make this software accessible for a wide range of companies to provide fast, accurate and objective three-dimensional virtual ergonomic tests analysis and design. By using Ergonocloud Software they will be able to create optimal working environments, workflows and products while maintaining the health of their employees and investing in their efficiency, competitiveness and sustainability.

Experiment Descriptions
Competence Centers
Digital Innovation Hub


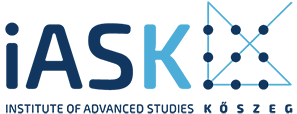
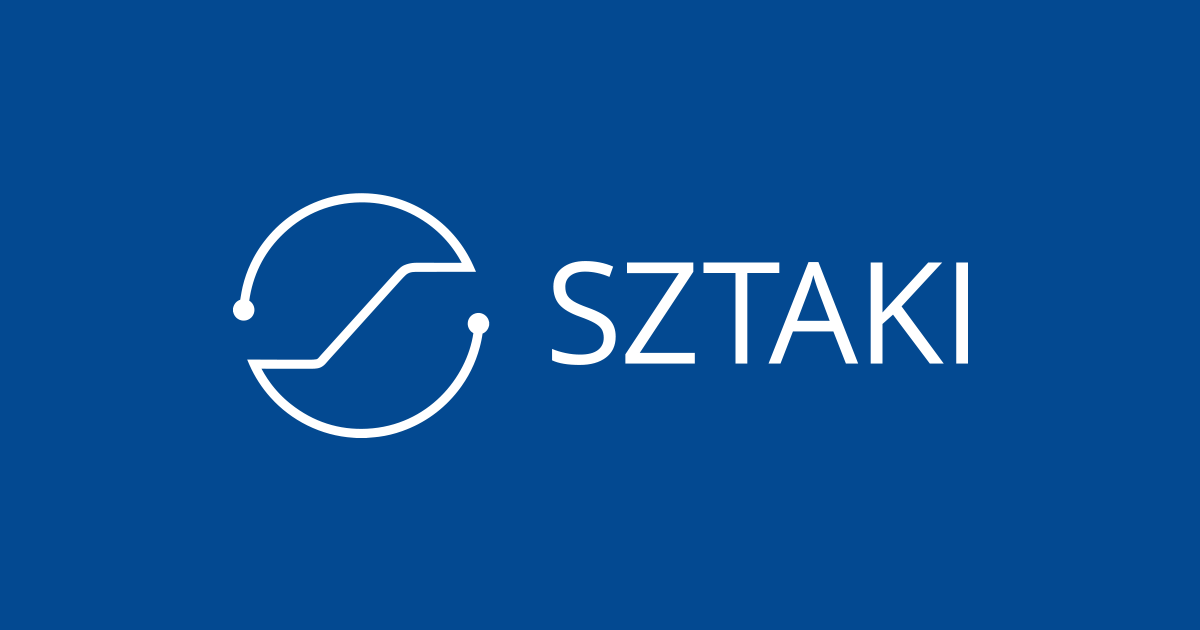
